Hiring surge represents hard-earned payoff for Austal USA
On the surface, Austal USA’s announcement last week that it plans to hire 1,200 people in the near future, growing its work force by more than 40%, seems like a story about what’s going to happen. But in a lot of ways, it’s a story about what has already happened.
“Austal has moved from one customer to six,” Austal USA President Rusty Murdaugh said at a Monday press conference announcing a major job fair that was to take place Saturday. “We’ve moved from building two types of ships to 13.”
He might have been underselling it.
It wasn’t that long ago that the Mobile shipyard was scrambling to find a future for itself. It had grown rapidly on the strength of two aluminum ships built for the U.S. Navy: The Independence-class Littoral Combat Ship (LCS), an angular aluminum trimaran, and the Expeditionary Fast Transport (EPF), a multipurpose aluminum catamaran. Its workforce had peaked at around 4,300.
But as the end of the LCS program drew closer, the need for work to follow it became more of a concern. The most coveted prize on offer was the contract to build a new generation of Navy frigates, a program that would have kept Austal’s yard busy for a decade. But in early 2020, the Navy chose another shipyard.
There was silver lining. Austal’s exclusive focus on aluminum shipbuilding was a constraint. The federal government gave Austal $50 million to offset the effects of the pandemic, and Austal matched that with another $50 million or so. The combined investment allowed Austal to diversify into steel shipbuilding and to pursue a much wider range of work.
Craig Perciavalle, then president of Austal USA, said in 2019 that the frigate contract was at the top of his wish list but Austal was gunning for a growing list of alternatives. Austal was pitching a medical version of the EPF, he said, and showing concepts for autonomous vessels that looked like robotic cousins to the EPF and LCS. Austal also was expanding its post-delivery work, including a San Diego office that had opened in 2018.
Adding a steel line opened up additional possibilities. Speaking to AL.com in August 2021, Larry Ryder, Austal USA’s vice president for business development and external affairs, ticked off some of them: The Navajo-class T-ATS salvage ship. The Coast Guard’s Offshore Patrol Cutter. A landing craft called the Light Amphibious Warship. Maybe there was even a shot at becoming a “follow yard” for the frigate, building copies of the winning design as the Navy sought to accelerate production. The work force was holding steady at 3,300, Ryder said at the time.
Since then, Austal has been steadily booking steel work. None of its individual wins stack up as high as its run of 19 Littoral Combat Ships, but collectively they add up. The first steel ship off the new line will be a T-ATS. It’s expected to be ready for delivery in late 2024, and Austal will build at least three more of the towing, rescue and salvage ships. The Navy has commissioned it to build a $128 million dry dock. Austal has even won work to build sections of nuclear submarines.
The biggest win by far came in June 2022, when Austal won a contract to build Heritage-class Offshore Patrol Cutters. Austal is a follow yard, and the cutters it builds will be based closely on the work of the Florida yard that won the initial contract. But the deal could be worth more than $3 billion if the Coast Guard exercises all its options. That would make it second only to the LCS program in Austal’s portfolio.
It’s not a moment too soon. The last Independence-class LCS, the future USS Pierre, is about 40% complete, Ryder said. “We’re actually closing up the LCS line,” he said.
In announcing Austal’s hiring campaign, Murdaugh said that Austal currently employs around 2,800 people. If not for the new work coming in, the shipyard would be bracing to see that number fall, rather than planning a surge that will take it back close to its historic high.
“All these projects are what drives the need for that hiring,” said Ryder.
What drives the projects? It might not be just the new steel line. For years, Austal leaders have claimed that they’ve pioneered a manufacturing process that sets their yard apart. LCSs and EPFs aren’t built in a traditional way. Major sections called modules are constructed separately, then welded together in the giant assembly halls that face downtown Mobile across the Mobile River.
In theory, it’s a process that brings modern manufacturing efficiencies to the one-hull-at-a-time world of shipbuilding, and Austal USA has regularly touted its ability to put out a lot of ships on schedule and within budget. It has been easy to discount that as hype, but the flood of new work suggests the Navy has been convinced it’s more.
U.S. Navy Chief of Naval Operations (CNO) Admiral Michael Gilday, center left, visits the Austal USA shipyard in Mobile on Jan. 26, 2023. According to Austal, Gilday “toured the shipyard’s facility and discussed the company’s growing diversity of design and shipbuilding contracts,” witnessing work on both steel and aluminum ships in the company’s 867,000-square-foot module manufacturing facility.Courtesy of Austal USA
“I think I could sell that to the Navy all day long,” said Ryder. “At the end of the day they’re going to say, are deliveries on schedule, on time? And we have been.”
“Our process gets us the results, the results are what the customers react to,” he said.
The fact that Austal USA is now helping build nuclear submarines may be the best illustration. It’s “something which would have been a pretty crazy thought a year ago,” Ryder said.
Other companies build the Virginia-class and Columbia-class submarines, and that isn’t changing. But Ryder said the Navy wants to make sure the industrial base is there to support its desired production rates, and that’s where Austal comes in. It knows how to build modules, so it’s going to be doing that: Command and Control Systems Modules and Electronic Deck Modules for the two sub programs.
Building the cylindrical pressure hull is the kind of specialized job Austal won’t be taking on. “What we build is going to slide into that hull as a module,” Ryder said. The process is beginning with a module being shipped in for Austal to outfit; by 2026 it’ll be building them from scratch and shipping them up the East Coast for installation.
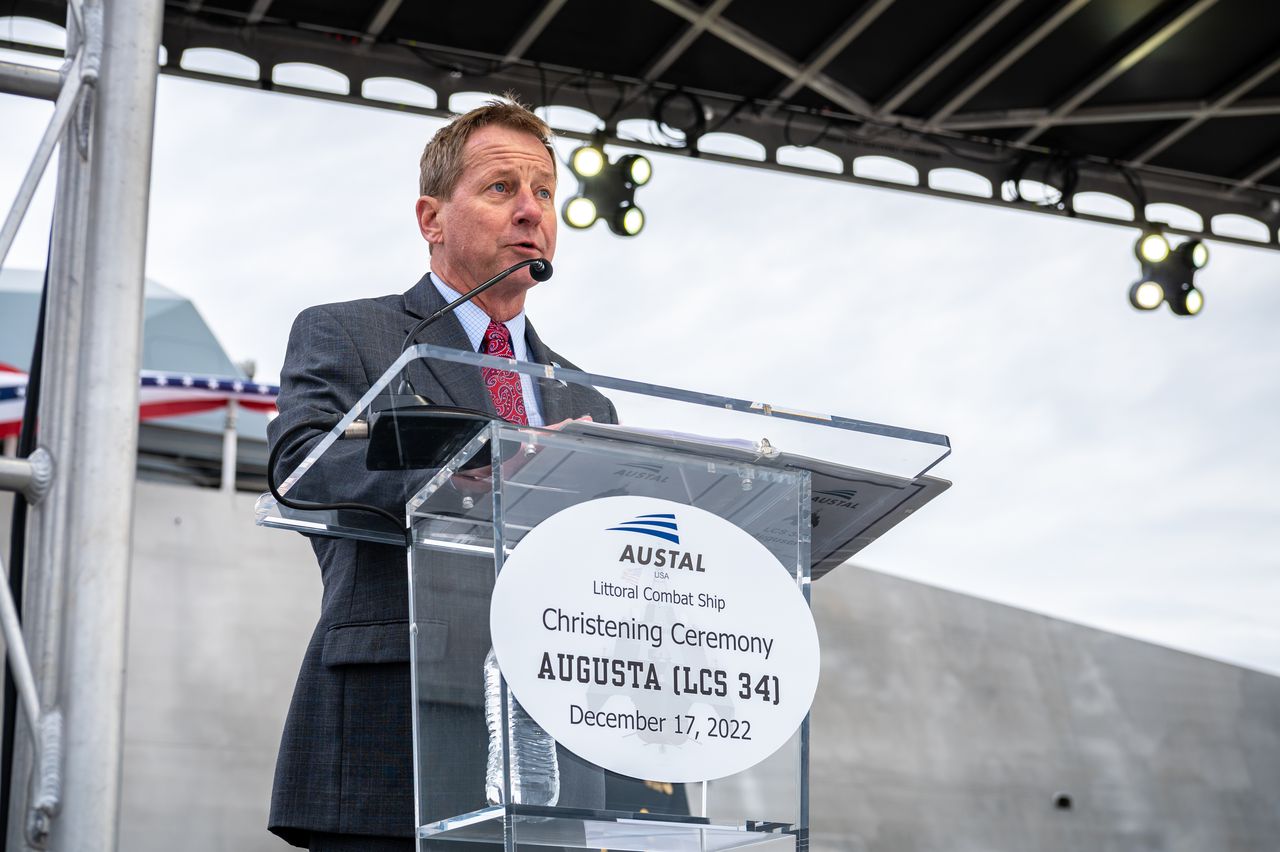
Larry Ryder, Austal USA’s vice president for business development and external affairs, speaks at the christening of a Littoral Combat Ship in December.Courtesy of Austal USA
“The way we’ve built our yard, it’s manifesting,” Ryder said.
“I don’t think there’s really a secret sauce,” he said. “It’s really a mentality, it’s a culture.”
“Each time we move a module, we have those meetings and say, ‘How could we do this better?’” he said. It’s all about considering changes that could improve efficiency. Tool placement? The way a module is designed, or simply the way it is positioned for the work? Cutting the time skilled workers spend on unskilled prep work? Can permanent lighting be installed early in the process, eliminating the need to add and then remove temporary lighting? The goal is to shave hours off the process.
Bridge modules in particular are nearly complete, with most electronics installed and tested, before they’re grafted onto ships, Ryder said. That contributes to ships being nearly complete when launched, requiring less outfitting, testing and troubleshooting than might otherwise be the case.
The growing workforce will have to be trained to handle an increasingly diverse range of projects. In addition to more EPFs, including medical ships, Austal will be building wind-propelled drones. The yard even has orders to construct the aluminum elevators that will lift jets to the decks of the next USS Enterprise and another new aircraft carrier, the future USS Doris Miller, Ryder said.
The yard will lean heavily on its corps of veterans with 5, 10, or 15 years under their belts, he said. “It’s really going to come down to leadership,” he said.
It’s a challenge on multiple levels, including workforce education. Bradley Byrne, president and CEO of the Mobile Chamber, said the hiring campaign is “not just an Austal effort. This has to be a community effort. This has to be an all-in effort.”
Winning the contracts means Mobile’s biggest industrial employer has turned a daunting corner. Now every contract in hand represents a promise that has to be delivered on.
“We’ll perform on those, we’ll do what we always do,” said Ryder. “We’ll probably be adding a couple of new buildings.”